Process
21 small test cups were thrown “off the hump” with studio clay and bisque fired to cone 04.
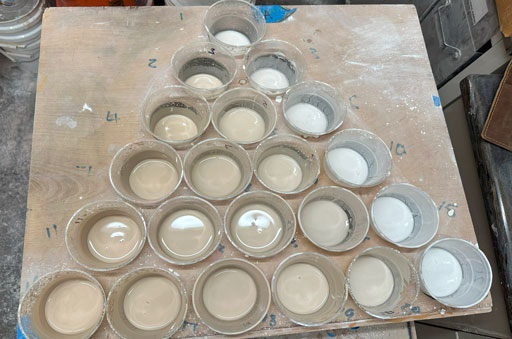
Test Glazes Prepared: Ingredient A: 800g of Custer (feldspar), Ingredient B: 400g Whiting & 400g Kaolin, Ingredient C: 400g Magnesium Carbonate & 400g Silica
Plastic glaze containers were filled per the Hopper handout, each contained a 100g blend of ingredients (A, B, and C). Water was added to the cups to create the glaze.
Glazing Test Cups: The ceramic test cups were dipped into the glazes and numbered to coincide with the numbers on the plastic containers using black underglaze.
These cups were fired to cone 10 in an reduction kiln.
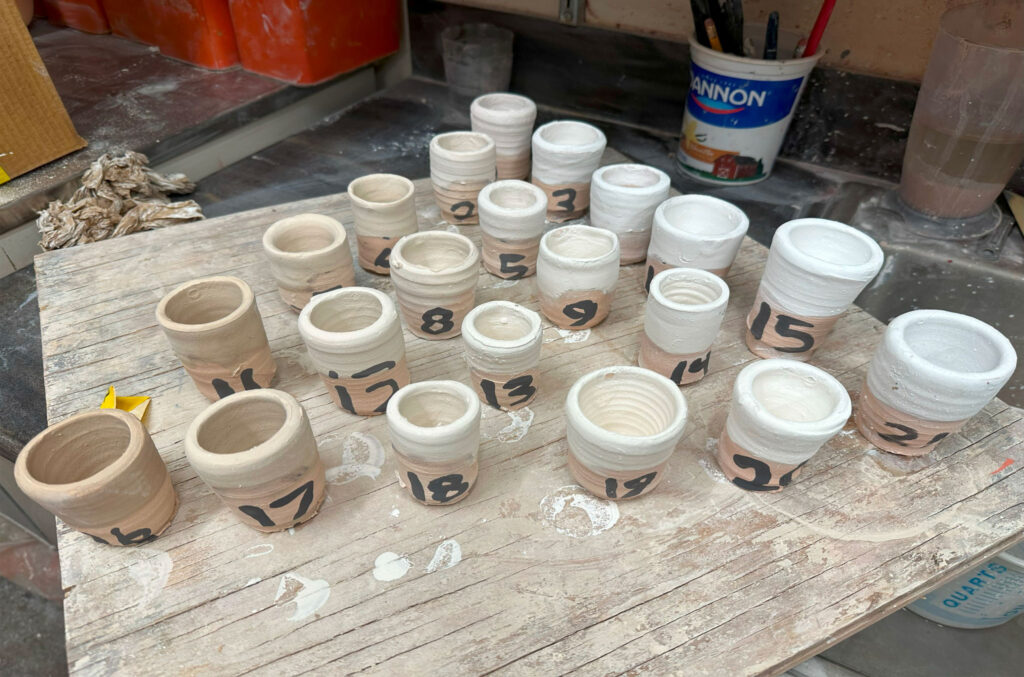
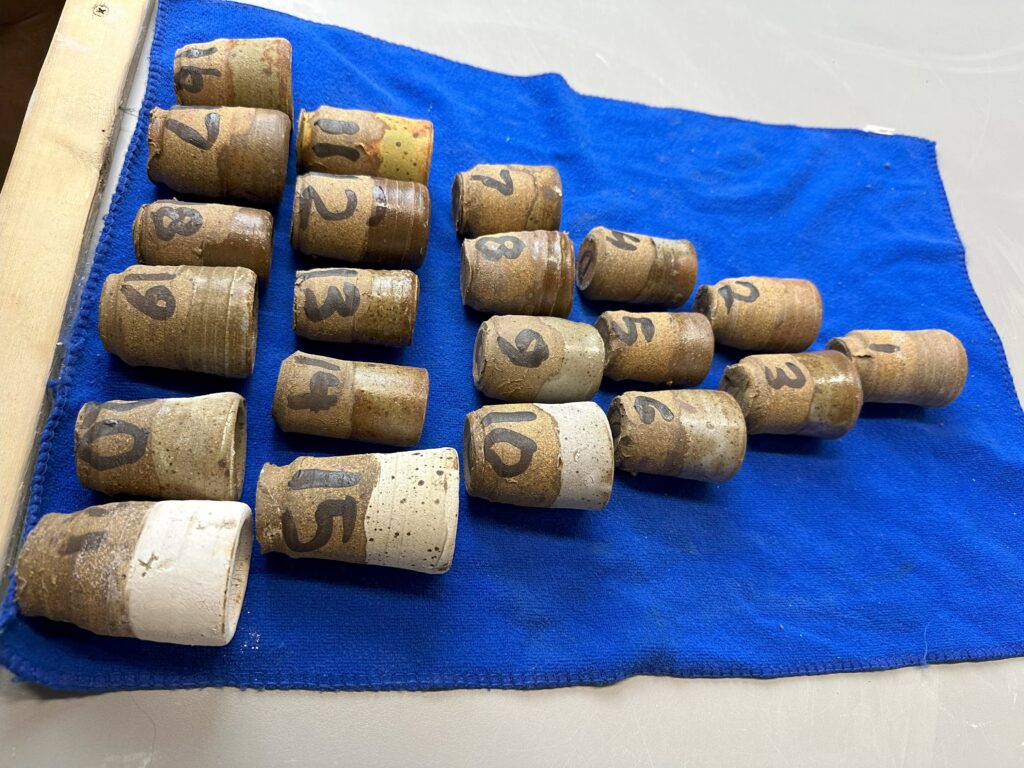
Glaze Evaluation: After the cups were fired, the appearance of each was evaluated and the most successful mix was selected to be used for the color test.
Test Glaze: To replicate the results on Test Cup 9, a 100g test glazed was prepared with the three ingredients: ( A: 40g Custer, B: 10g Whiting & 10g Kaolin, and C: 20g Magnesium Carbonate & 20g Silica) Water was added, and the glaze was applied to a bisque-fired cup. The cup was fired in a cone 10 reduction kiln and the results were as expected. Note the image to the left.
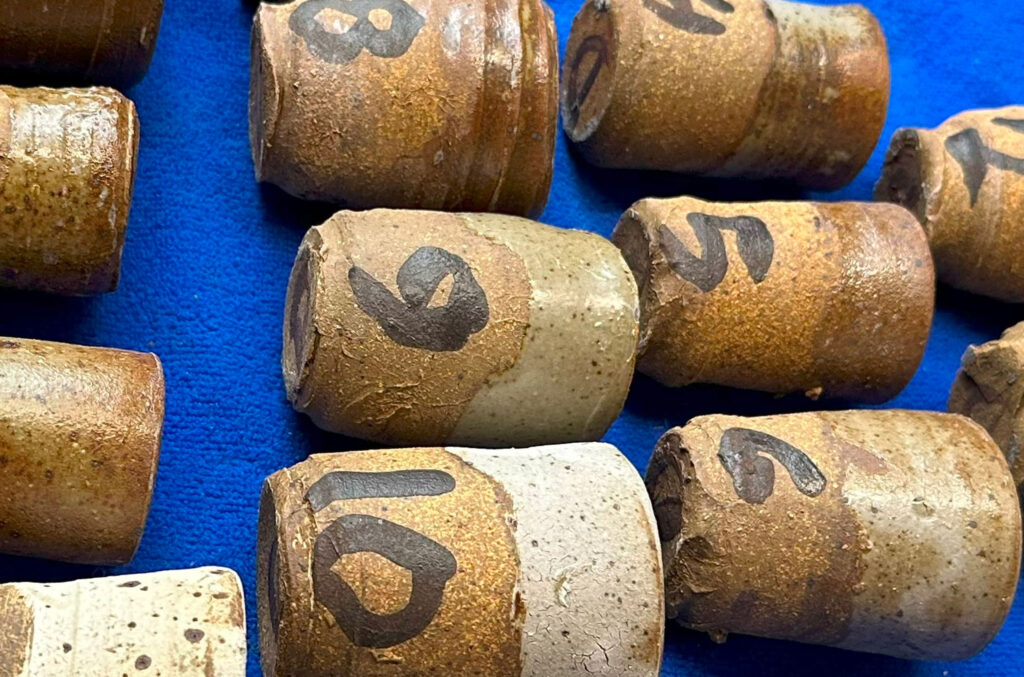
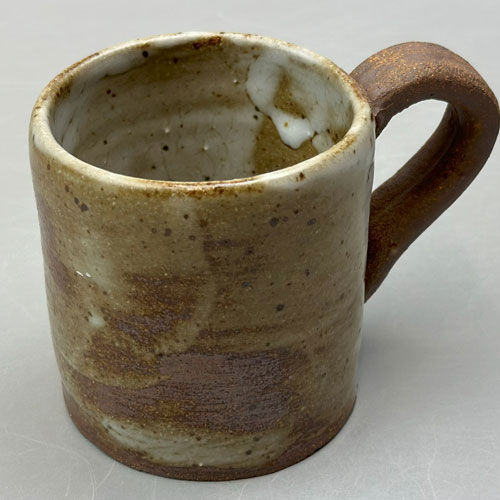
Test Cup Results: The glaze had a semigloss finish, and ran in areas where the glaze was applied a little thicker.
This glaze mix was used for the Modifying a Glaze Color Test
A Look into Feldspars & Fluxes
While feldspars are a type of flux, not all fluxes are feldspars. Here’s the breakdown:
Feldspars
The name feldspar is German and means field stone. They make up about 60% of Earth’s crust and are highly adaptable due to their diverse crystallography and chemistry. These naturally occurring minerals, comprising sodium, potassium, and calcium aluminosilicates, are crucial in ceramics. They provide alumina and silica, helping to form a glassy phase during firing.
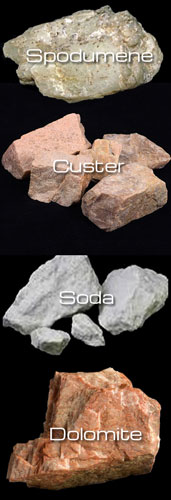
Potash Feldspars (Potassium Feldspars):
Custer Feldspar: Widely used in the United States, known for its consistency.
G-200 Feldspar: Another popular potash feldspar, often used interchangeably with Custer.
Cornwall Stone: Contains both potassium and sodium, used in high-fire glazes1.
Soda Feldspars (Sodium Feldspars):
Soda Feldspar: General term for feldspars with a high sodium content.
Nepheline Syenite: Contains both soda and potash feldspars, plus nepheline, a sodium aluminum silicate1.
Kona F-4 Feldspar: A common soda feldspar used in the United States2.
Lithium Feldspars:
Spodumene: Contains lithium, used for its unique fluxing properties.
Petalite: Another lithium feldspar, often used in crystalline glazes1.
Mixed Feldspars:
Volcanic Ash: Contains a mix of potassium and sodium feldspars, though its composition can vary1.
Fluxes
This is a broader category that includes any material added to a glaze to lower its melting temperature. Besides feldspars, fluxes can also be materials like whiting (calcium carbonate), zinc oxide, lead oxide, and others. This is not a complete list of Fluxes.
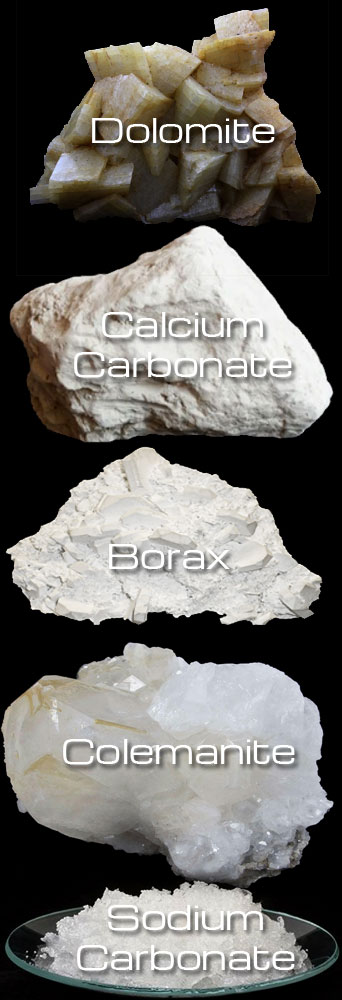
Sodium Fluxes:
Soda Feldspar: Commonly used in mid- to high-fire ranges.
Nepheline Syenite: A high soda feldspar with some potassium, useful in mid-range temperatures.
Sodium Carbonate (Soda Ash): Used in various glaze recipes.
Sodium Chloride (Table Salt): Used in salt firing and vapor glazing1.
Potassium Fluxes:
Potash Feldspars: Such as Custer and G-200, preferred for high-fire glazes.
Cornwall Stone: Contains potassium, sodium, and calcium.
Volcanic Ash: Rich in potassium, though its composition can vary1.
Lithium Fluxes:
Lithium Feldspars: Such as spodumene and petalite.
Lithium Carbonate: Encourages crystal growth in crystalline glazes1.
Boron Fluxes:
Gerstley Borate: Though no longer mined, some limited amounts are still available.
Colemanite: Often used in raku glazes.
Borax: Used to smooth out higher firing glazes.
Boron-containing Frits: Such as Ferro 3110, 3124, and 31341.
Calcium Fluxes:
Whiting (Calcium Carbonate): Used in high-fire glazes.
Dolomite: A calcium-magnesium carbonate used in high-fire glazes1.
Magnesium Fluxes:
Talc: Often used in low-fire glazes.
Magnesium Carbonate: Used to produce matte surfaces2.These fluxes help lower the melting point of the glaze materials, making them easier to apply and achieve desired effects during the firing process.